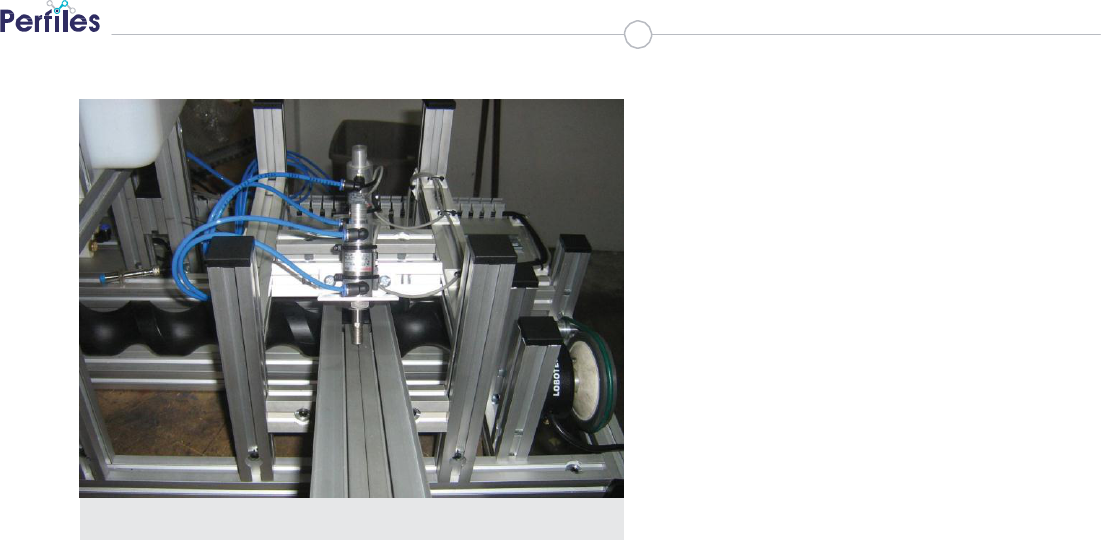
Figura 9. Sistema de colocación de tapas
con el cilindro ubicado perpendicularmente al tarro en la
misma posición.
Una vez realizado el proceso de colocación y sellado de
tapas, es necesario que el recipiente cumpla con el ciclo
y sea llevado hasta el final de la línea de producción, para
lo cual es accionado una vez más el gusano transportador.
Como segunda parte del desarrollo del proyecto, está la
implementación del software para el SCADA.
El HMI es un sistema amigable con el usuario, lo más
completo, simplificado y fácil de navegar (7).
El proceso simula un sistema industrial real de envasado
volumétrico, por lo que la autenticación de usuarios per-
mite asignar las funciones y permisos definidos para cada
uno de los perfiles.
La gran mayoría de los sistemas SCADA están basados
principalmente en mecanismos de autentificación auto-
matizados basados en usuario/contraseña. La asignación
de cuentas dependerá de dos factores importantes: el área
de responsabilidad junto con permisos y privilegios asig-
nados a un operador, y el tiempo de actividad según lo
prefijado en su contrato. Para el control de cuentas acti-
vas como inactivas (tanto por expiración como por baja
de contrato), el sistema deberá ejecutar frecuentemente
un procedimiento de análisis para comprobar en términos
de tiempo la validez de las credenciales de seguridad, y
cualquier cambio asociado al usuario deberá ser registra-
do. Asimismo, cualquier tipo de actividad en una sesión
debe ser igualmente registrada para facilitar posteriores
procesos de análisis (por ejemplo, estadísticos o foren-
ses). Las credenciales de seguridad deberán estar fre-
cuentemente actualizadas siguiendo unos patrones y una
política fuerte de control de accesos. El sistema deberá
bloquear todas aquellas cuentas que sobrepasen un cier-
to umbral de intentos fallidos, limitar el
número de sesiones por usuario y evitar
el envío de credenciales de seguridad en
claro usando mecanismos criptográficos
(6).
Para este caso se tienen planteados 3
perfiles de usuarios.
Invitado: como su nombre lo indica, es
un perfil que simula una persona que no
tendrá permisos para realizar acciones
de control o supervisión sobre el proce-
so; lo único a lo que tendrá acceso es la
visualización del desarrollo del proceso,
pero no podrá cambiar ningún paráme-
tro del mismo.
Operador: este usuario puede ingre-
sar a la etapa de supervisión y realizar
los cambios operativos dentro del pro-
ceso; estos permisos incluyen cam-
bios en el volumen que será deposi-
tado en el recipiente, reconocimiento
de alarmas, encendido y apagado del
proceso.
Ingeniero: este perfil de usuario tie-
ne los permisos para acceder a todas
las opciones del proceso y desarrollar
cambios operativos, así como tam-
bién acceder a las opciones de segu-
ridad del sistema (bypass), y cambiar
de modo manual a modo automático y
viceversa.
Una vez definidos los perfiles de
usuarios, la estructura del programa
consta de:
• Autentificación de usuarios, tres ni-
veles de permisos (invitado, opera-
dores e ingenieros).
• Visualización de datos de nivel de
líquido para dosificar, recipientes,
tapas, velocidad del proceso, canti-
dad de producto terminado, fallos del
proceso, etc.
• Generación de reportes en Excel.
• Base de datos que guarda la infor-
mación de alarmas, eventos, usua-
rios y productos terminados desde el
InTouch.
ISSN 1390-5740 Número 14 Vol. 2 (2015)
ISSN 2477-9105