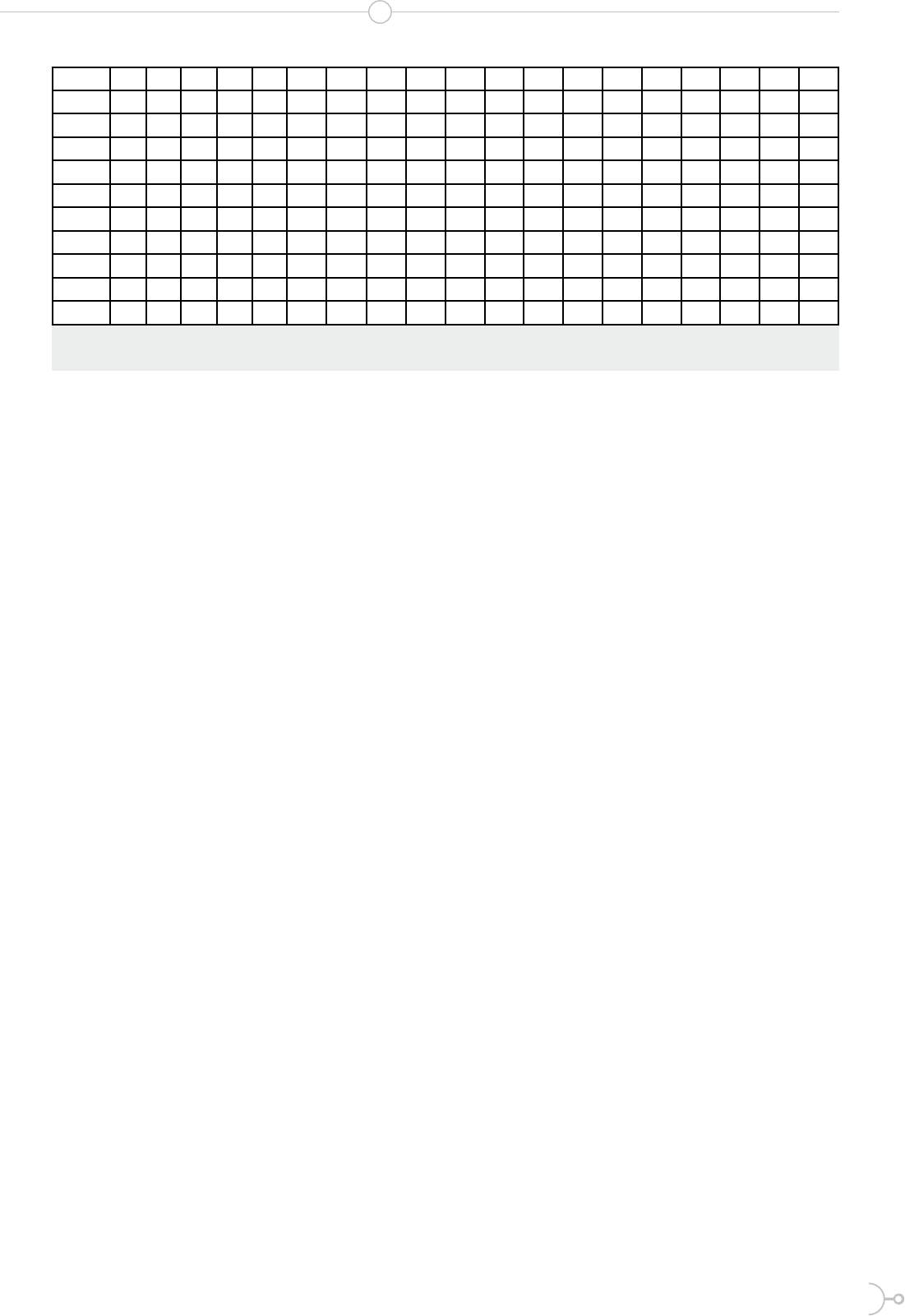
51
Gallegos Londoño, Calderón Freire, Viscaíno Cuzco, Villacrés Parra
ensayo o de soporte; aprovisionamiento
de piezas de recambio; instalaciones re-
queridas (2,18,19). La determinación
apropiada de los recursos necesarios,
provocará la disminución de los retardos
logísticos. El objetivo de este artículo es
presentar el indicador probabilístico con
un ejemplo práctico a nivel industrial
visto desde varias aristas y el desarrollo
de un indicador que evalúe los retardos
logísticos y administrativos que afectan
a la mantenibilidad global.
II. MATERIALES Y MÉTODOS.
Mantenibilidad probabilística. Los da-
tos para el análisis fueron tomados de
históricos de los tiempos operativos de
las reparaciones registrados en órdenes
de trabajo del departamento de mante-
nimiento, fueron recopilados por un pe-
ríodo de diez meses, en una muestra de
91 grupos electrógenos de tres marcas
distintas, tabla 6
El análisis probabilístico de la manteni-
bilidad se lo realizó utilizando la distri-
bución de Weibull. Primero se calculó
la mantenibilidad global, se tomó en
cuenta a todos los grupos electrógenos.
El análisis se lo realizó con una frecuen-
cia mensual. Para el estudio se tomaron
cuatro tiempos de referencia (probabili-
dad de reparación a las: 2, 10, 20 y 40
horas). En segundo lugar se realizó el
Eventos 1 2 3 4 5 6 7 8 9 10 11 12 13 14 15 16 17 18 19
Mes 1
0,3 0,5 0,5 0,7 1,0 1,5 1,7 2,0 2,0 2,5 2,5 2,5 4,0 6,3 22,5 - - - -
Mes 2
0,5 0,8 1,0 2,0 2,0 3,0 10,5 15,4 16,8 17,2 17,3 17,3 20,5 22,2 22,3 22,5 22,5 - -
Mes 3
0,3 0,5 0,5 1,0 1,0 3,5 5,0 5,0 6,0 7,6 7,8 8,1 8,3 16,6 17,9 19,8 19,8 21,7 -
Mes 4
1,0 1,6 2,0 6,0 8,5 9,0 9,2 9,9 10,0 19,9 21,5 21,7 22,2 22,2 23,2 - - - -
Mes 5
1,4 3,0 4,5 5,0 6,0 8,8 9,0 9,9 10,5 11,7 15,1 15,9 18,3 21,2 21,7 22,6 23,3 - -
Mes 6
0,3 0,7 1,0 2,0 2,8 3,3 5,0 8,0 16,1 21,0 21,4 - - - - - - - -
Mes 7
1,0 2,0 3,1 4,1 5,1 8,1 9,2 11,2 11,2 12,2 16,3 - - - - - - - -
Mes 8
1,0 2,0 2,0 3,0 3,1 4,5 6,0 7,0 8,3 8,7 9,0 9,7 10,5 11,2 14,1 21,2 79,4 - -
Mes 9
0,3 1,2 2,0 3,0 4,0 4,0 7,8 10,8 13,0 15,0 21,9 47,5 56,0 74,5 - - - - -
Mes 10
1,1 3,0 6,0 7,4 7,9 8,0 8,0 8,0 8,5 9,6 10,3 10,3 10,6 14,8 16,3 17,5 19,5 20,2 24,0
Tabla 6. Lista de tiempos de reparación por mes
cálculo probabilístico de la mantenibilidad por marca,
se reorganizaron los tiempos de reparación tomando en
cuenta las marcas de los equipos, el propósito de este es-
tudio en particular fue determinar cuál de las tres marcas
analizadas tiene mejores probabilidades de reparación.
Para nalizar con el análisis probabilístico se hizo otra
variante, se calculó la mantenibilidad por tipo de falla,
se reorganizaron nuevamente los tiempos de reparación
considerando ahora las fallas mecánicas, eléctricas y
electrónicas, se utilizó este análisis para determinar qué
tipo de fallas tienen mayor probabilidad de reparación.
En todos los casos se realizó las pruebas de bondad (coe-
cientes de correlación y determinación) (20,16).
Como se ha mencionado el tiempo de reparación de una
falla se divide esencialmente en dos, el tiempo técnico de
la reparación y el tiempo de los retardos logísticos y ad-
ministrativos. Para el cálculo del indicador probabilístico
de la mantenibilidad se utilizan los tiempos de reparación
(3,10), quedando fuera de este análisis los tiempos de los
retardos logísticos y administrativos, a pesar de que algu-
nos de estos tiempos son exógenos a las acciones técni-
cas de mantenimiento, deben ser evaluados pues afectan
directamente a la disponibilidad operacional de los equi-
pos (21).
Los retardos logísticos y administrativos descritos en la
tabla 5 son de índole variada, algunos de sus valores
pueden variar desproporcionadamente dependiendo de
factores externos al mantenimiento como: estrategias
gerenciales, mercados externos, negociaciones con pro-
veedores de materiales y repuestos, etc. Para evaluar los
retardos logísticos y administrativos se propone la utili-
zación de un algoritmo similar al utilizado en la norma
española UNE 151001 (1), utilizada para la evaluación
de los atributos de diseño de los dispositivos industria-
les. Este algoritmo sirve para evaluar varios criterios de